Improving soldering time, quality and repeatability using UltraFlex Induction Heating — UltraFlex Power Technologies
UltraFlex Power Technologies showed how a coaxial cables hand soldering process could be replaced with induction soldering
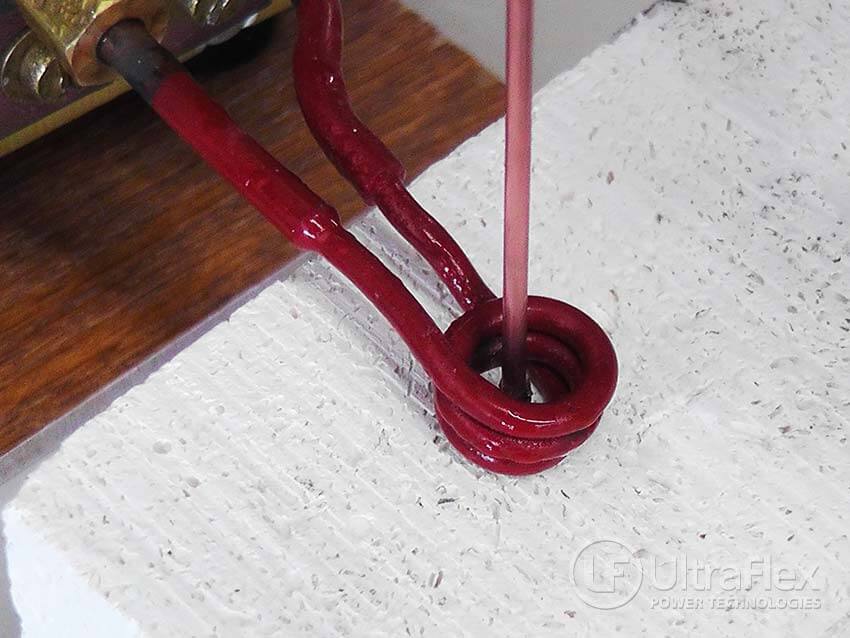
Soldering using UltraFlex induction heating
NEW YORK – Nov. 24, 2017 – PRLog — In a recent customer-requested demonstration, UltraFlex Power Technologies showed how a coaxial cables hand soldering process could be replaced with induction soldering to improve quality, repeatability and to minimize the time needed for each connector assembly.
The goal of the demonstration was to solder coaxial cables to copper connectors using induction heating, evaluating the performance of two UltraFlex Induction Heating systems – Ultraheat SB-3 with maximum power output of 3 kW and Ultraheat SH 2-350 with maximum power output of 2 kW. A custom induction coil had been designed to optimize the heating for this specific application. The target temperature for the soldering process was ~400°F (204°C).
Couple of tests were done with each of the 2 kW and 3 kW Heating systems – one test using flex cable and a brass ferrule and another test using solid copper lead and a brass ferrule.
In the demonstration, a low temperature solder 63/37 wire was used. Light coating of solder flux was added to the wire and lead, on place of the originally used “rosin core solder” (flux in the core) which was unavailable in UltraFlex lab at that time.
A pre-formed wrap of the alloy was made to fit the diameter of the lead wire (flexible or solid). The assembly base (ferrule assembly) was located in the coil with the ferrule portion set approximately in line with with the lower coil turn.
Using the high-frequency SB-3 power supply, at a frequency of 742 kHz and using only 0.24 kW of the available 3 kW power, the time needed to solder the joint was 2.4 seconds when flex cable was used and 3 seconds when solid copper lead was used.
Using the high-frequency SH 2-350 power supply, at a frequency of 300 kHz and using power of only 0.4 kW out of the available 2 kW, the heating time needed to affect the solder flow and joint was 3 seconds wfv for the flex lead and 4 seconds for the solid copper lead.
Equal time to the heat cycle is then needed to ensure the molten alloy has solidified prior to removing the assembly from the load-coil.
These two tests showed that the induction-based soldering process could be successfully completed using a less expensive 2 kW Induction Heating unit, while greatly improving the heating process time-wise. The use of a pre-formed alloy ring would ensure that the process is repeatable and uses an equal amount of alloy for each joint, resulting in quality end finish on every assembly made.
About UltraFlex Power Technologies:
Ultraflex Power Technologies (https://ultraflexpower.com) manufactures and sells induction heating power supplies. Induction power supplies generate a precise, targeted electromagnetic field that induces heat in conductive materials without the need for a flame or any contact with the material.
An induction heating system consists of an induction power supply and a custom-designed inductor (also known as a coil). The induction power supplies are universal systems, with custom coils designed to optimize the heating process for the specific application. These systems can be used for heating conductive materials in variety of applications ranging from metal melting and heat-treating to medical and nanoparticle research.