Toulouse Space Show Exhibit to Celebrate 60th Anniversary of OmniSeal RACO Spring-Energized Seal — Saint-Gobain Seals
Saint-Gobain Seals is exhibiting at the Toulouse Space Show in France to share their sealing and polymer solutions as well as celebrate the 60th anniversary of their OmniSeal® RACO® spring-energized seal.
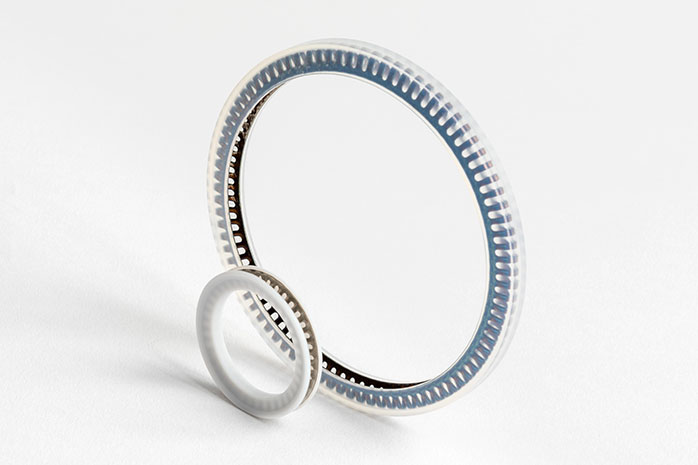
60th Anniversary of OmniSeal RACO Spring-Energized Seals
GARDEN GROVE, Calif. – May 22, 2018 – PRLog — Saint-Gobain Seals is exhibiting at the Toulouse Space Show from June 26 to 28, Booth #C3, to share their sealing and polymer solutions as well as celebrate the 60th anniversary of their OmniSeal® RACO® spring-energized seal. Organized in cooperation with CNES (French Space Research Centre), the event is attended by more than 3,000 worldwide participants and is a major global forum dedicated to novel space solutions that highlight future trends and the new space economy.
Selected for many space applications because of its precise fit and lifetime confidence, the RACO® seal was developed in the 1950s and was a part of NASA’s early space programs such as Mercury and Gemini followed by the Apollo and Shuttle programs. Saint-
One of the key reasons that the RACO® spring-energized seal has been selected in the past 60 years is due to its proven success rate in space applications with challenging conditions. An example would be cryogenic applications in launch vehicle propulsion systems where propellants are stored at cryogenic temperature such as liquid oxygen (-320°F/-196°
Available in various fluoropolymer grades and meeting chemical compatibility requirements in the space industry (liquid oxygen and hypergolic fluids), the RACO® seal can be manufactured in a wide range of sizes that make it ideal for different applications, e.g., rocket tanks that can be a few meters large or much smaller valves, and feeding lines that transfer fuel to the rocket engine.
Over the past few years, there has been a surge in the commercialization of the space industry, leading to different requirements and procedures versus those of government agencies. These new changes result in demands for rapid design iterations, design engineering and lower flight costs. To manage these needs, Saint-Gobain Seals closely collaborates with its space customers and uses their FEA and R&D capabilities to support and co-develop new solutions for critical sealing parts.
Along with the OmniSeal® (https://www.seals.saint-
To learn more about Saint-Gobain Seals’ OmniSeal® product line, other product lines and its strategic business unit, visit http://www.seals.saint-
About Saint-Gobain Seals (http://www.seals.saint-
Saint-Gobain Seals is a strategic business unit under Saint-Gobain Performance Plastics’ Engineered Components SOA (sector of activity); our parent company, Saint-Gobain, is one of the world’s top 100 industrial groups as well as one of the oldest manufacturing companies in the world with 350 years of excellence. With more than 50 years of manufacturing experience and an established global presence (with strategic sites in Garden Grove, California, USA; Kontich, Belgium; and Minhang, Shanghai, China), we offer a diverse range of critical parts for extreme applications.